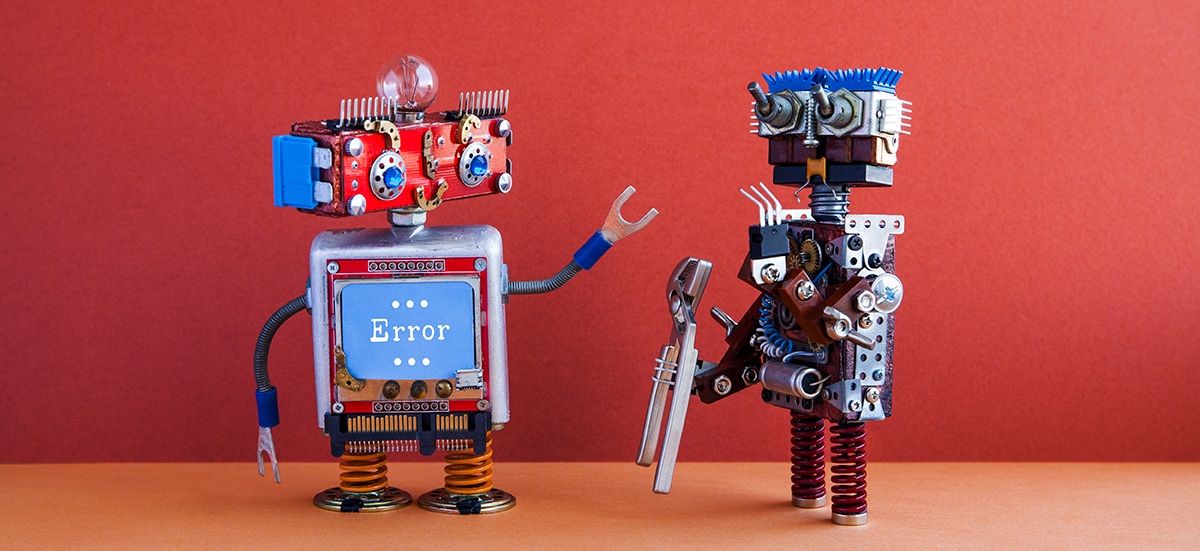
Workforce and Automation in the Australian Meat Industry
Becoming increasingly prominent in the red meat industry, the issue of labour remains one of the biggest challenges faced in today’s world of meat processing. The Australian Meat Industry Council (AMIC) considers the problem to be critical and has labelled it a ‘Labour Deficit Epidemic’, an issue which has swept across rural Australia, preventing almost two thirds of Australia’s red meat processors from running at capacity.
In 2018, AMIC conducted a survey to identify issues facing the industry with the shortage of labour identified as the second-greatest problem faced by the industry – only exceeded by livestock production. A truly grim prospect; there is an average of a 20 per cent labour shortage throughout the entire industry.
So, what will this wealth of underlying obstructions mean for the future of the meat industry?
At present, it becomes an increasing prominent challenge that must be met if companies want to experience sustained growth. With about 72 per cent of Australian red meat produced being exported, the industry’s long-term sustainability relies heavily on our ability to remain competitive in international markets.
Analysis from Australian Meat Processor Corporation (AMPC) has shown that processors in Australia are faced with operational costs (excluding livestock) between 1.5 and 2.8 times higher than our key international competitors. Labour therefore plays a critical part in our bid to remain viable overseas.
“the use of machines, as opposed to human hands, the risk of product contamination and food spoilage is greatly reduced.”
There are several possible solutions being developed to address this growing concern. One of the most promising avenues for resolving this issue is the adoption of robotics and intelligent machinery.
Many of the more repetitive, even dangerous tasks requiring unskilled labour in the industry are being automated. Automation increases both the speed and accuracy at which the tasks can be completed. US figures show that in 2018, the known injury rate for meat workers was the highest recorded across all areas of manufacturing. Unsurprising; given the often sharp and pointy objects that meat preparation processes revolve around. Automation presents a clear prospect to make this industry less of a glaring OHS nightmare.
Furthermore, with the use of machines, as opposed to human hands, the risk of product contamination and food spoilage is greatly reduced. Overall, if ever there was a perfect job for robots, it’s cutting up carcasses 24/7 – it requires little-to-no critical thinking, and the machines can often complete this efficiently, more uniformly and far more safely.
Many innovative experts in meat processing facilities of all size – from family butchers to large abattoirs have realised the potential, a more intelligent breed of machines has to offer.
“This technology has done wonders for large and small-scale producers in the industry…”
This innovative machinery has become available in the Australian Meat Industry, with products such as the Treif Dicer and Automatic Hamburger Machines accessible to smaller independent butchers, currently facing the affects of the labour deficit.
Stuart Mead, General Manager of Viking Food Solutions speaks of the positive supplement this automated machinery has for his customers. “This technology has done wonders for large and small-scale producers in the industry, a cost-effective solution for meat processors. The equipment has, in the past, not been so accessible to smaller, independent butchers due to cost and availability. We’re proud here at Viking Food Solutions to bridge this gap and provide such solutions to our customers like the Treif Dicer and Automatic Hamburger Machine.”
The Treif Dicer allows you to accurately dice meat, choosing within a millimetre the size of the dice required, which traditionally was a manual tasks, requiring a high level of skill and time. The Viking Automatic Hamburger Machine forms up to 2100 patties/hour, uniform size and shapes.
Like adding in any other major equipment to the processing facilities, maintenance and servicing is required to ensure that the machinery continues to operate at capacity and safely for staff and customers alike.
The dependence of automation within the meat processing industry has raised some questions about the future of a skilled workforce. A recent report by Adzuna suggests that about a third of jobs across all industries is predicted will be replaced by robotics within the next 12 years.
With an industry currently facing such a labour deficit, the use of robotics and automation presents a valuable solution, both short and long-term. Allowing for employees to approach high-level job tasks, leaving tasks with high levels of repetition to robotics.
We have arrived at a time of significant change in the red meat industry. Both large processors and small-scale butchers alike are forced to adapt to shifting conditions, to remain competitive in a new workforce climate. However, the consensus seems to be that smarter machinery to replace a dwindling workforce will be the way of the future. And if this presents significant challenges for many in the industry, it provides significant opportunity too.
Equipping the food industry to grow with food processing and packaging solutions
call 1300 88 99 51
email [email protected]
room 35 Shirley Way, Epping VIC 3076
room 9 Mcilwraith St, Wetherill Park NSW 2164
room 21 Hoyle Rd, Hope Valley WA 6165
room 27 Beal Street, Meadowbrook QLD 4131
room 7 Chadderton Bvd, Epping VIC 3076
room 22 Glassford Rd, Kewdale WA 6105
room 25 Hayton Road, Wigram, Christchurch 8042, NZ
Connect with us on LinkedIn
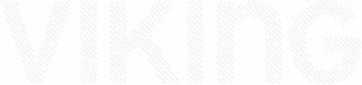