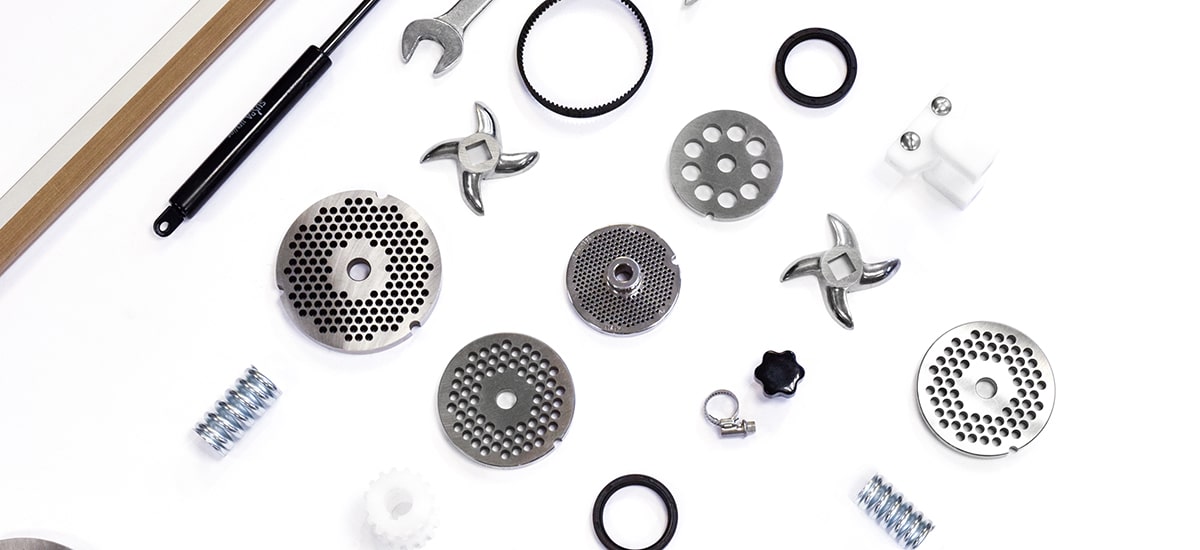
Why you should service your food processing machinery?
Whether you’ve got bandsaws, slicers, tray sealers or vacuum packers – all machinery used in your day-to-day operations requires a service now and again to ensure that it is operating at peak efficiency for your business – why?
Like your car or air-conditioner, the machinery that you use daily requires a check up to ensure that all the working components, parts and functions are working safely for you and your staff.
Will the efficiency of our machines increase after a service?
Sometimes during a routine service, our technician may identify that there may be a blockage or issue affecting the efficiency of the machine, with a quick service and some TLC, your machinery will be back to its original working condition in no time!
Preventative maintenance
Like the term suggests, this maintenance is to take a proactive approach to ensuring that all your machinery is running smoothly before anything were to malfunction and cause you any further damage along the track.
This will lessen the likelihood of any future issues occurring unexpectedly. Meaning that in the middle of peak trading, you can rest assured that your slicer or dicer isn’t going to stop unexpectedly!
Spare parts
Sometimes you can replace parts yourself and don’t really need to go to the trouble of booking in a service callout for your machinery.
We understand this and have a dedicated spare parts team ready to take your order and ship parts to your door, giving you all the tools, you need to do some D.I.Y on your equipment.
Equipping the food industry to grow with food processing and packaging solutions
call 1300 88 99 51
email [email protected]
room 35 Shirley Way, Epping VIC 3076
room 9 Mcilwraith St, Wetherill Park NSW 2164
room 21 Hoyle Rd, Hope Valley WA 6165
room 27 Beal Street, Meadowbrook QLD 4131
room 7 Chadderton Bvd, Epping VIC 3076
room 22 Glassford Rd, Kewdale WA 6105
room 25 Hayton Road, Wigram, Christchurch 8042, NZ
Connect with us on LinkedIn
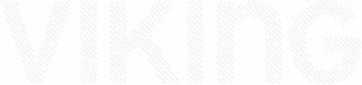