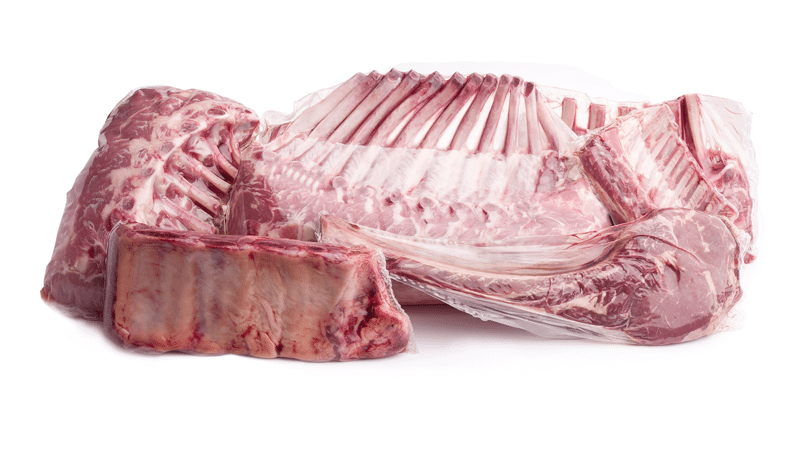
Supermarket Shrink Bags
2025 sustainability targets draws near, high volume users of plastic packaging such as supermarkets and meat processors are preparing for a shift in their soft plastics supply.
With a large proportion of products being packaged in shrink and vacuum pouches for shelf-life extension and preservation, these users of plastic require suppliers with a high level of competency and ability to undergo intensive testing to prove compatibility.
The testing for this involves fit for purpose, category and on-site testing before the product packaging is approved and moved into circulation.
Supermarkets must critically assess their suppliers products and packaging to ensure that the materials will not only perform but surpass the criteria.
Fit for purpose testing
This is the first step of the rigorous testing procedure suppliers undergo, and this stage will determine whether suppliers’ products will perform under extreme conditions.
Why? There are critical steps within the supply chain to get products from source to shelf, and often, these conditions are quite testing.
To ensure the products remain fit for consumption, meat packed in the shrink bags are put under a 42-day shelf-life trial and this is conducted at the meat supplier’s plant. These are tested against control bags of standard material, along with this ‘challenge bags’ are tested in deliberately high conditions – some up to 8°C and there are also some tested under standard, expected storage conditions.
After this 42-day trial period, the bags are opened, packaging and product inside checked every few days to check for abnormalities in appearance, integrity, odour, taste and purge.
The Viking team are pleased to share that we have participated in and passed fit for purpose testing in these environments with our Viking Shrink Bag Range.
Category Testing
Products are packed in the same material as the successful bags from the first stage of testing and sent to the supermarket facility.
At this facility, the products are observed for a month and audited by trained staff, who note any anomalies and non-standard microbiological counts.
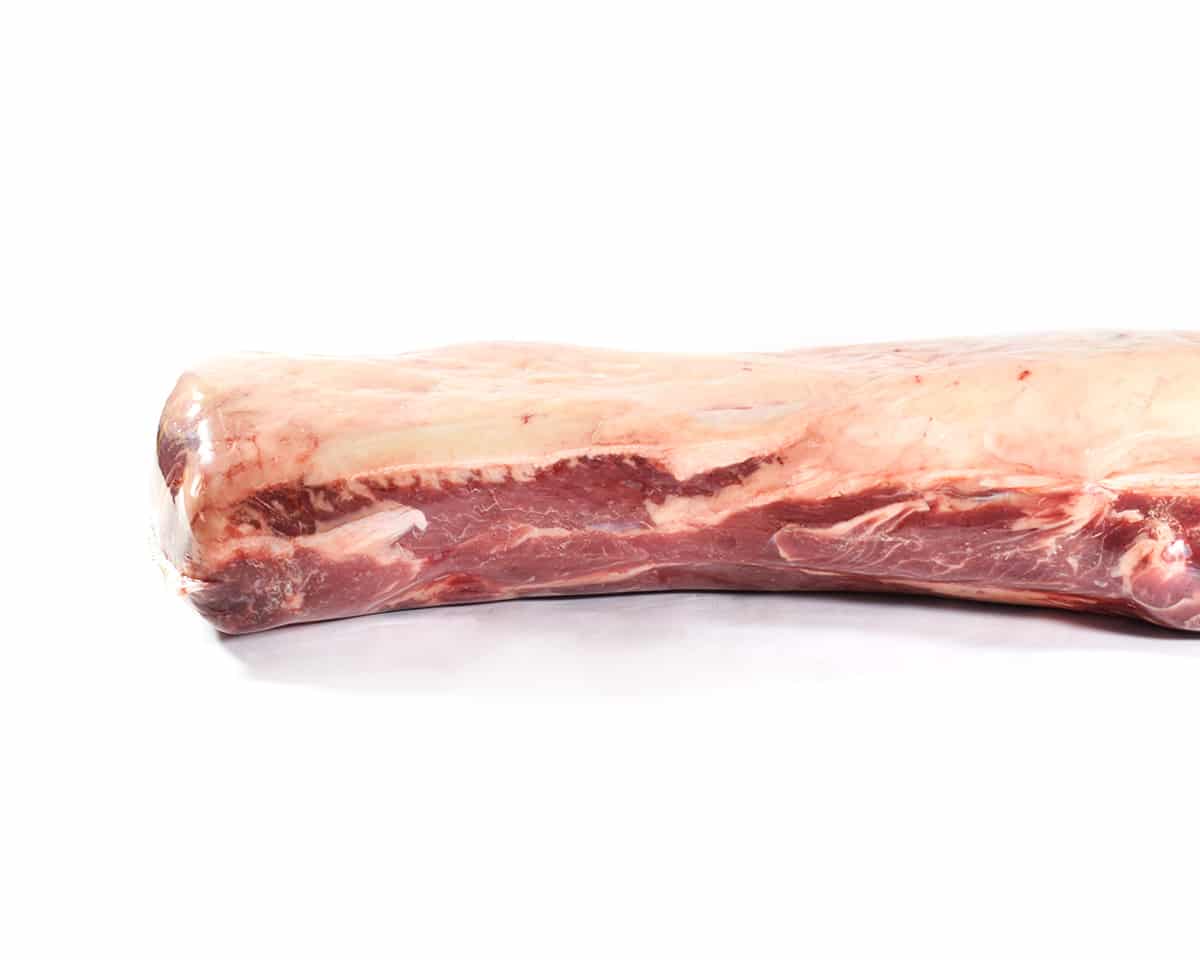
On-site supermarket testing
Once the products have passed Category Testing, in order to verify results in standard sale conditions, on-site supermarket testing then takes place where test products are placed on the shelf for real customers to purchase.
This is at a select number of supermarkets within the group, where staff observe the performance of the products – whether customers are purchasing the new line, and record returns and customer complaints.
If the product then passes this final stage of testing, the product becomes fully approved for use.
We’re very pleased to share that our shrink bags have been through all rounds of testing including fit for purpose, category and on-site for major Australian supermarket retailers.
Our dedicated QA Team are well-versed in all aspects of soft plastic guidelines and are well equipped to take our customers through their testing procedure, supplying all information relating to materials in rigid and flexible plastics.

Equipping the food industry to grow with food processing and packaging solutions
call 1300 88 99 51
email [email protected]
room 35 Shirley Way, Epping VIC 3076
room 9 Mcilwraith St, Wetherill Park NSW 2164
room 21 Hoyle Rd, Hope Valley WA 6165
room 27 Beal Street, Meadowbrook QLD 4131
room 7 Chadderton Bvd, Epping VIC 3076
room 22 Glassford Rd, Kewdale WA 6105
room 25 Hayton Road, Wigram, Christchurch 8042, NZ
Connect with us on LinkedIn
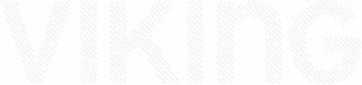