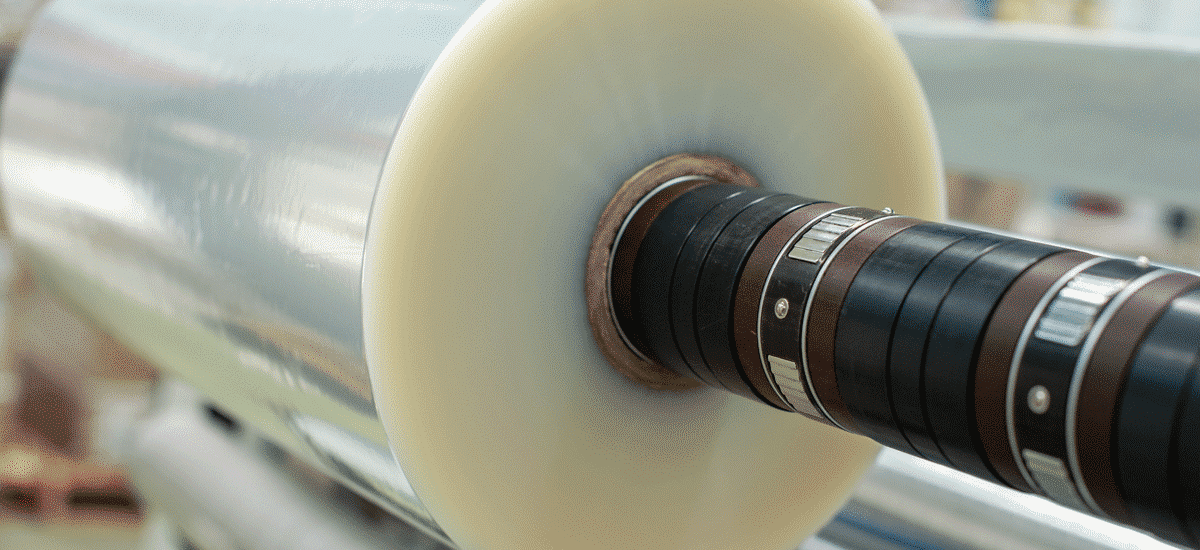
Flow Wrapping
The shrink flow-wrapping packaging technique provides a great method of packaging products rapidly, effectively and with full automation.
The flow wrapping process – unlike thermoforming packaging systems – only requires one roll of film. The machine wraps this film sheet around the product, sealing it with a fin seal to enclose the product. It is then run through an auto-indexing seal bar which simultaneously seals the ends of the packs and cuts them apart to form the individual packages.
These packages are then run through a hot air shrink tunnel, tightening the polyolefin shrink film against the product. For this reason, many processors prefer pre-perforated film, as the micro holes allow the air in the sealed packs to escape more easily as the polyolefin contracts, creating a tighter visual appearance around the product. Another solution is the perforation roller attachment for the flow-wrapping line.
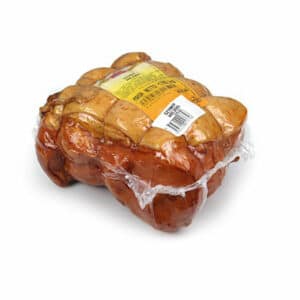
What is Flow Wrapping used for?
Flow wrapping is a swift and straightforward method to provide a basic level of protection for your product, and therefore has a wide range of applications.
Typically, is used for frozen or export products – often frozen lamb – IW (Individually-Wrapped) packaging automation, dried pet food products and where appearance and hygiene is critical for meat and protein products. This versatile process can be used to pack off a vast array of products.
What are the benefits of Flow Wrapping?
The primary positive of shrink flow wrapping technology is time-saving, freeing up labour units on the packing line for more profitable tasks. Using this method rapidly increases the production throughput of any processing line.
The process is completely automated from start to finish. No manual labour involvement minimises risk of QA fault, bringing consistency to each pack.
A further benefit is the environmentally friendly aspect.
Compared to other puncture resistant packaging, shrink polyolefin film uses 75% less plastic.
What is Polyolefin?
Polyolefin is a premium shrink material supplied by Viking to the meat-processing industry and is both extremely versatile and durable. It is a mono plastic film commonly used for flow-wrapping.
The advantage of Polyolefin is the strength structure combined with high-shrink memory within only 15-25 microns of thickness.
Furthermore, the monolayer structure categorises Polyolefin as a sustainable material, easily sorted and processed by recycling systems, unlike other plastics with multi-layer structures. It is a material already suited to Australia’s evolving circular economy and acceptable in our soft plastic recycling streams.
Limitations of Flow-Wrapping
Shrink flow-wrapping frozen meat products does not focus on creating consumer ready packaging with extended shelf-life and should not be used for such.
Multi-layer shrink bags combined with vacuum packing technology should be used when seeking to achieve extended shelf-life.
Shrink flow wrapping – with its high efficiency and complete automation – has been revolutionising packaging lines in many boning rooms and export meat plants.
If you believe this system has potential for your product, speak with our team on how you can incorporate Polyolefin into your workflow.
Equipping the food industry to grow with food processing and packaging solutions
call 1300 88 99 51
email [email protected]
room 35 Shirley Way, Epping VIC 3076
room 9 Mcilwraith St, Wetherill Park NSW 2164
room 21 Hoyle Rd, Hope Valley WA 6165
room 27 Beal Street, Meadowbrook QLD 4131
room 7 Chadderton Bvd, Epping VIC 3076
room 22 Glassford Rd, Kewdale WA 6105
room 25 Hayton Road, Wigram, Christchurch 8042, NZ
Connect with us on LinkedIn
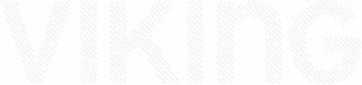